Tower Packing: Factors Influencing Selection and Design, and Advancements for Efficiency and Sustainability
Tower packing plays a crucial role in various chemical process industries, including petroleum refining, petrochemical production, gas processing, and environmental protection. It serves as a vital component in separation, absorption, and distillation processes within industrial towers and columns. The selection and design of tower packing are influenced by several factors, ranging from the specific process requirements to the properties of the fluid or gas being processed. Furthermore, advancements in tower packing technology have led to improved process efficiency and environmental sustainability, driving its widespread adoption in modern industrial applications.
Factors Influencing Selection and Design:
Process Requirements: Different tower packing materials and designs are selected based on the specific process requirements, such as separation efficiency, pressure drop limitations, and heat transfer capabilities. The choice of packing influences the overall tower performance and the quality of the desired product.
Mass Transfer Efficiency: Tower packing is primarily utilized for mass transfer processes like absorption, distillation, and extraction. The selection of the appropriate packing material and design directly impacts the efficiency of mass transfer and ultimately affects the separation or purification process.
Chemical Compatibility: The tower packing material must be compatible with the chemicals or substances present in the process stream. Compatibility ensures that the packing material remains stable and does not degrade or contaminate the process fluid, ensuring operational safety and product quality.
Pressure Drop: Pressure drop is a critical consideration in tower packing design, as excessive pressure drop can result in decreased efficiency and increased operating costs. Proper selection of packing geometry and material can help maintain an optimal pressure drop for efficient process operation.
Fouling and Scaling Resistance: Some industrial processes involve substances that may lead to fouling or scaling on the surface of the packing material. Choosing packing with resistance to fouling and scaling ensures prolonged service life and reduced maintenance requirements.
Advancements in Tower Packing Technology:
Improved Packing Materials: Advancements in materials science have led to the development of new packing materials with enhanced properties. Modern packing materials offer higher mass transfer efficiency, chemical resistance, mechanical strength, and thermal stability, contributing to improved tower performance.
Structured Packing Designs: Structured packing is an innovation that has gained popularity due to its superior performance in mass transfer and pressure drop reduction. These packing elements consist of corrugated sheets or profiles that provide a large surface area for interaction between the process fluid and vapor phase, leading to improved efficiency.
Random Packing Designs: Traditional random packing materials, such as ceramic, metal, or plastic, have been optimized through research and advanced manufacturing techniques. Novel surface geometries and specialized shapes have been developed to enhance mass transfer characteristics and reduce pressure drop.
Computational Fluid Dynamics (CFD) Modeling: CFD simulations are now widely used to optimize tower packing designs. By simulating fluid flow and mass transfer within packed columns, engineers can better understand the performance of various packing configurations and select the most efficient design for a given application.
Environmental Considerations: Modern tower packing technology also emphasizes environmental sustainability. Packed columns are used in applications like gas scrubbing and wastewater treatment to remove pollutants and harmful emissions from industrial processes, contributing to cleaner air and water.
In conclusion, the selection and design of tower packing in chemical process industries are influenced by a combination of process requirements, mass transfer efficiency, chemical compatibility, pressure drop considerations, and resistance to fouling and scaling. Advancements in tower packing technology, including improved materials, structured packing designs, random packing optimization, CFD modeling, and environmental considerations, have led to more efficient and sustainable industrial processes. As the demand for efficiency, safety, and environmental responsibility continues to grow, advancements in tower packing technology will play a crucial role in shaping the future of chemical process industries.
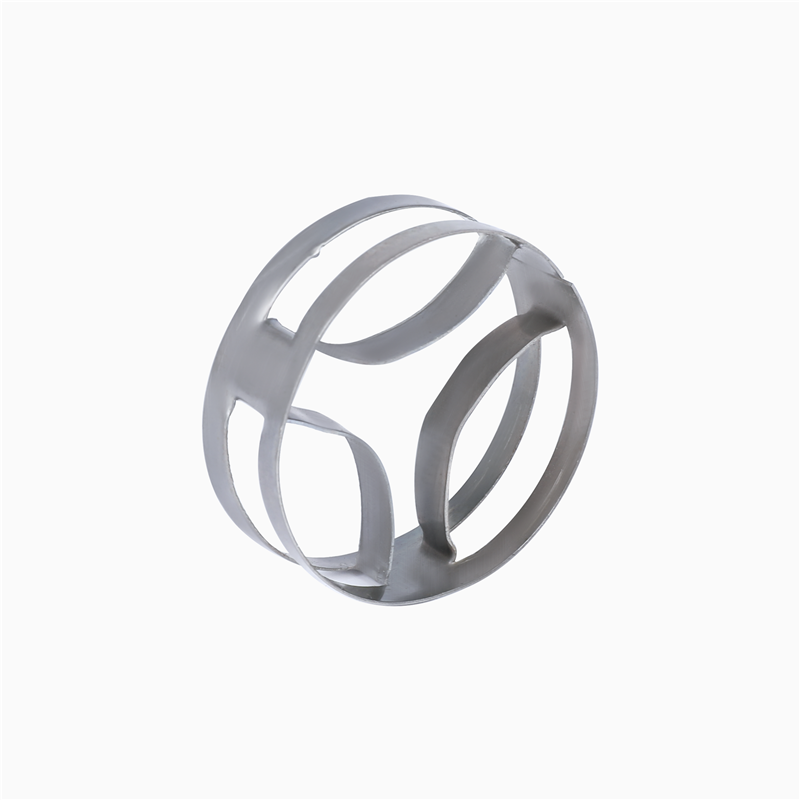
SUPER MINI RING PACKING
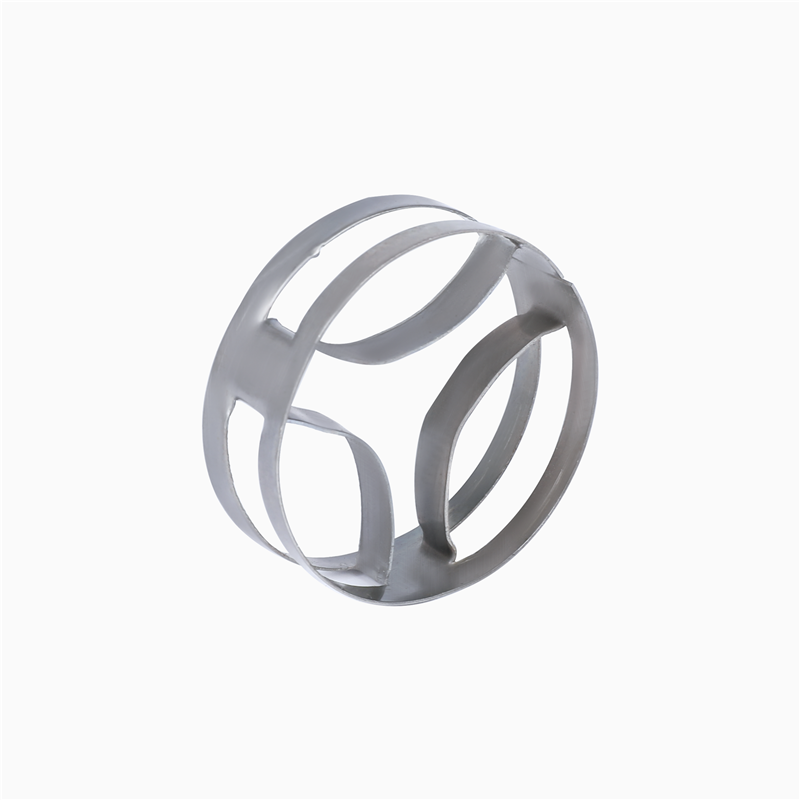
SUPER MINI RING PACKING