Metal Random Packing: Advantages and Comparative Performance in Chemical Processing Applications
Metal random packing is a critical component used in various chemical processing applications, particularly in distillation, absorption, and reactive mass transfer processes. It serves as an efficient medium for gas-liquid contact and mass transfer within packed columns, towers, and reactors. As a highly versatile and widely used packing material, understanding its key advantages and comparing its design and performance to other types of tower packing materials sheds light on the reasons behind its prevalence in the chemical processing industry.
Advantages of Metal Random Packing:
High Efficiency and Performance: Metal random packing provides a large surface area for gas-liquid contact, promoting efficient mass transfer between phases. Its open structure allows for uniform distribution of fluids, ensuring high efficiency in separation, distillation, and absorption processes. The design of metal random packing enables optimal use of tower space, leading to compact and cost-effective equipment designs.
Corrosion and Temperature Resistance: Metal random packing materials, such as stainless steel, Inconel, and titanium, offer excellent corrosion resistance to various chemicals and aggressive process fluids. This characteristic makes metal packing suitable for handling corrosive, high-temperature, and challenging operating environments, ensuring long-term reliability and performance.
Mechanical Strength and Durability: Metal random packing is known for its mechanical strength and robustness. It can withstand high compression loads without significant deformation or breakage, providing stability and longevity to packed columns, even under high-pressure conditions.
High Capacity and Scalability: The design of metal random packing allows for high-capacity towers, making it suitable for handling large gas and liquid flow rates. This feature is particularly beneficial in industrial-scale applications where large throughput and scalability are essential.
Low Pressure Drop: Metal random packing is engineered to have a low-pressure drop across the packed column. This characteristic reduces energy consumption and operating costs, making it an attractive option for processes that require efficient mass transfer with minimal energy expenditure.
Comparative Performance with Other Packing Materials:
Metal vs. Plastic Random Packing: Compared to plastic random packing, metal packing generally offers higher mechanical strength, corrosion resistance, and temperature tolerance. Plastic packings are more suitable for applications involving less corrosive fluids or in cases where cost is a significant factor. However, in harsh or high-temperature environments, metal random packing outperforms plastic in terms of longevity and reliability.
Metal vs. Ceramic Random Packing: Metal random packing typically exhibits better mechanical strength and thermal conductivity than ceramic packing. While ceramic packing may be suitable for specific applications that require resistance to thermal shock or chemically inert behavior, metal packing offers a broader range of advantages, especially in applications involving corrosive and high-temperature processes.
Metal vs. Structured Packing: Compared to structured packing, which consists of arranged corrugated sheets, metal random packing offers higher void space and reduced pressure drop. Structured packing may be preferred when specific surface area requirements are critical, but metal random packing excels in high-capacity and low-pressure drop applications.
Metal vs. Ceramic Saddles: Metal random packing, such as metal saddles, is often favored over ceramic saddles due to its superior mechanical strength, higher capacity, and better corrosion resistance. While ceramic saddles may be suitable for certain low-demand applications, metal saddles are generally preferred for their robustness and broader range of applications.
In conclusion, metal random packing stands out in the chemical processing industry due to its numerous advantages, including high efficiency, corrosion and temperature resistance, mechanical strength, and low-pressure drop. Its design and performance offer distinct benefits compared to other packing materials like plastic, ceramic, structured packing, and ceramic saddles. The versatility and reliability of metal random packing make it a preferred choice for chemical engineers and plant operators seeking efficient and durable mass transfer solutions in various gas-liquid processes. As advancements in materials and manufacturing techniques continue, metal random packing is expected to maintain its prominent role in driving process efficiency and reliability in chemical processing applications.
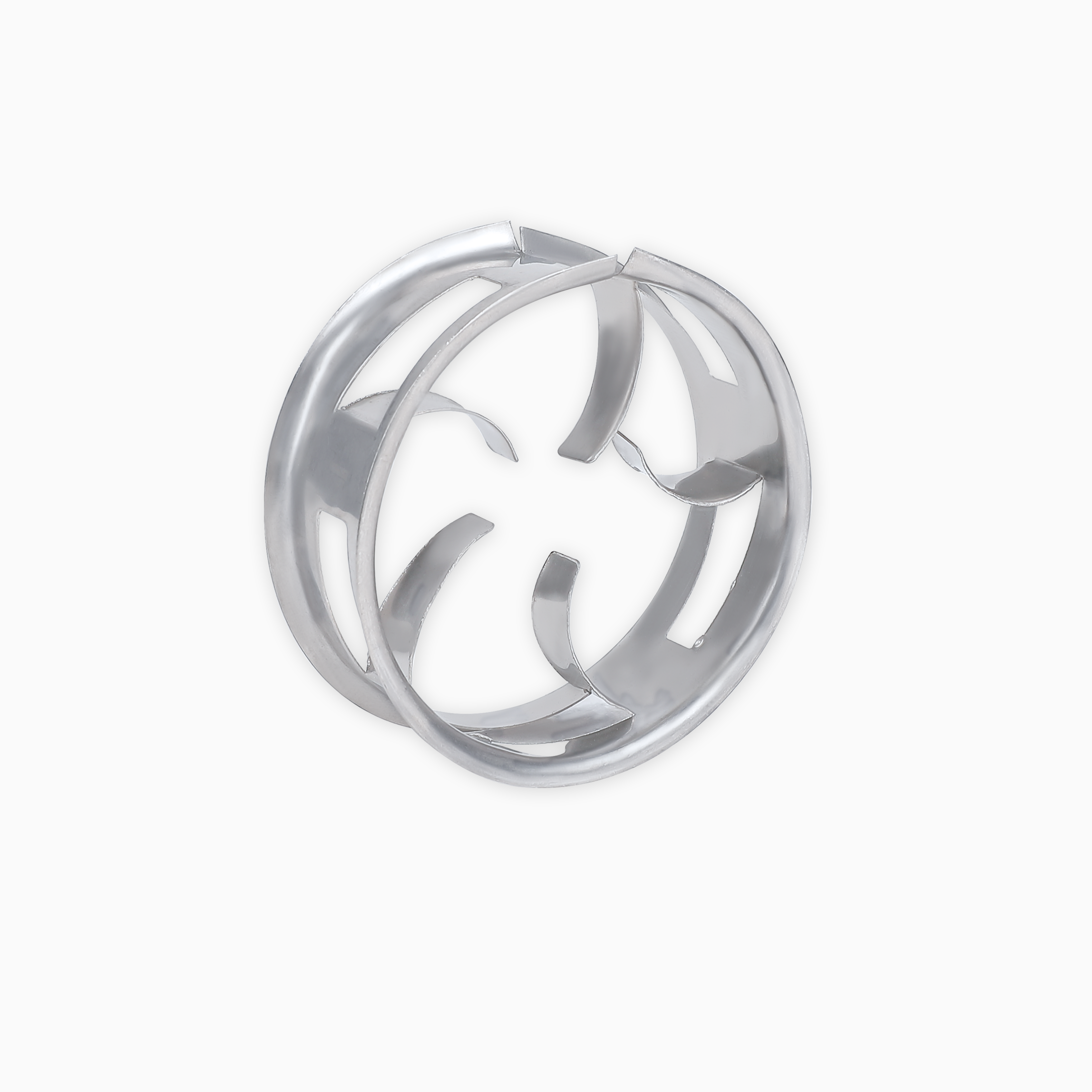
METAL CASCADE MINI RING
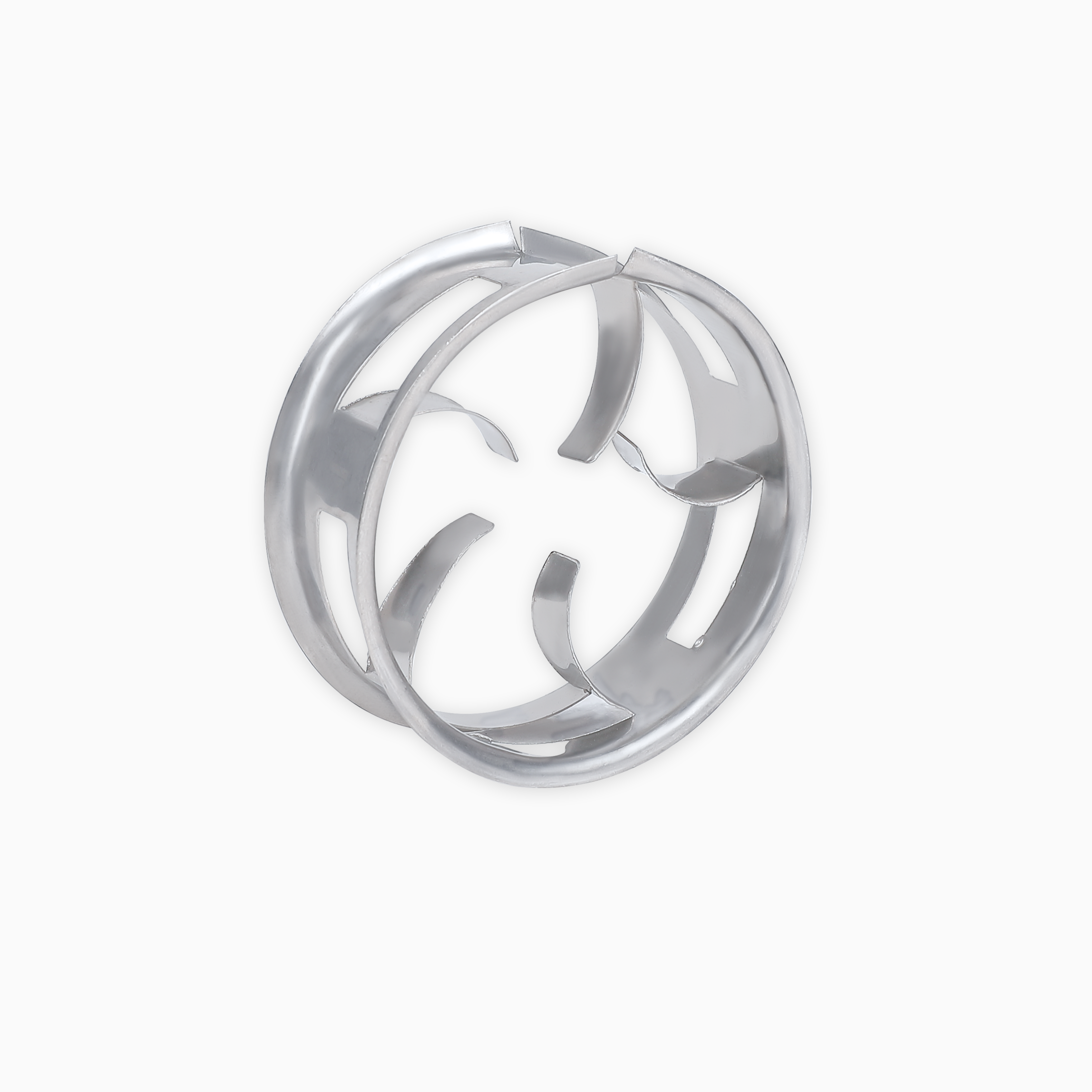
METAL CASCADE MINI RING